L’électrolyse alcaline est un procédé de production d’hydrogène robuste et éprouvé, et a démontré de solides performances à l’échelle industrielle. Cette technologie s’impose comme la pierre angulaire qui rendra possible la massification de la production d’hydrogène bas-carbone pour décarboner tous les pans de l’industrie.
Augmented McLyzer : architectures 16, 100 MW et au-delà (GW), à 30 bar
McPhy soutient la transition des secteurs de l’industrie, la mobilité et l’énergie vers une économie à faible émission de carbone, permettant aux clients de s’affranchir des énergies fossiles par la production massive d’hydrogène bas-carbone à des prix compétitifs. Dans cet objectif, nos électrolyseurs “Augmented McLyzer”, véritable rupture technologique sur le marché, allient la fiabilité et la maturité de la technologie alcaline haute pression à une flexibilité optimale. Ils sont intégrés dans nos conceptions de plateformes d’électrolyse très grande capacité (multi MW), spécifiquement dédiées aux secteurs de l’industrie et des transports lourds.
Technologie sélectionnée pour équiper le projet « Djewels » : une des plus grande unités (20 MW) à être implantée en Europe
McPhy a lancé en 2018 sa technologie révolutionnaire « Augmented McLyzer », une combinaison unique entre notre longue expertise de l’électrolyse alcaline haute pression et l’intégration d’électrodes de nouvelle génération à haute densité de courant (doublée par rapport aux électrodes standards) qui augmentent considérablement les performances de nos équipements, le tout dans un design compact.
Cette solution totalement modularisée intègre un design de modules 1 / 4 / 16 / 100+ MW , utilisés comme des « briques » de construction. Nos systèmes Augmented McLyzer produisent un hydrogène bas-carbone directement à haute pression (30 bar), et sont conçus pour passer à l’échelle au même rythme que vos activités.
Modèles | Pression (barg) | Débit nominal H2 (Nm3/h) | Puissance nominale | Conso. spécifique DC au débit nominal (kWh/Nm3) |
---|---|---|---|---|
McLyzer 800-30 | 30 | 800 | ca. 4 MW | 4,65 |
McLyzer 3200-30 | 30 | 3200 | ca. 16 MW | 4.65 |
Focus technologique
- Haute efficacité énergétique
- Compétitivité économique : meilleur TCO (Total Cost of Ownership) de sa catégorie, avec une pression de fonctionnement 30 bar, qui réduit significativement le besoin en compression.
- “Bigger scale, lower costs” : le déploiement à très grande échelle des applications hydrogène va rendre possible une réduction drastique des coûts
- Sécurité : Les équipements McPhy sont développés en intégrant les études de sécurité poussées (HAZOP, LOPA, études SIL, etc.), permettant d’atteindre les exigences de sécurités requises dans l’industrie chimique et Oil&Gas.
- Flexibilité et service aux réseaux: Compatible avec les services réseaux de la réserve primaire, les équipements McPhy de la gamme McLyzer s’adaptent aux changement de consigne en quelques secondes sur une plage de fonctionnement étendue (turn-down 20%-100%), ce qui les rend compatibles avec un couplage avec des sources d’énergie renouvelable.
- Modularisation : une architecture compacte, modularisée et évolutive, basée sur un « core-module » de 4 MW, utilisé comme brique de construction
- Disponibilité et longévité: la durée de vie du stack est corroborée par des résultats de tests en situation représentative. La disponibilité des équipements McPhy (> 96%) est adossée à un contrat de service (LTSA)
- Facilité d’installation: stacks et unité process (EPU) sont réalisés par McPhy sont livrés testés sur site pour assemblage par le client.
- Facilité d’opération: produits entièrement automatisés, et aux plateformes de visualisation et d’exploitation des paramètres opératoires (McView)
- Fiabilité d’exécution: grâce aux lignes de production automatisées et aux partenariats avec ses fournisseurs clés.
Domaines d’application
Cette gamme multi-MW est spécifiquement conçue pour la décarbonation à grande échelle des secteurs de l’industrie, de la mobilité et de l’énergie :
- Raffineries de pétrole et de gaz : désulfuration des carburants, e-fuels, etc.
- Traitement chimique : méthanol, synthèse d’ammoniac pour les engrais, etc.
- Et aussi : aciéries, centrales au charbon, centrales thermiques (système de refroidissement des alternateurs), métallurgie, production de verre, composants électroniques, etc.
- Stations hydrogène grande capacité : non seulement pour les grandes flottes captives (véhicules utilitaires ou stations publiques pour les voitures particulières), mais aussi pour recharger les modes de transport lourds (tels que les bus, les camions, les trains, les bateaux, etc.).
Zoom sur une réalisation
Djewels
McPhy a été sélectionné début 2020 pour équiper la plus grande unité de production d’hydrogène bas-carbone en Europe.
Capacité de production annuelle de 3 000 tonnes d’hydrogène bas-carbone (20 MW), 27 000 tonnes d’émission de CO2 évitées.
Un projet mené par Nouryon et Gasunie, deux groupes industriels majeurs, installé au cœur d’un parc chimique aux Pays-Bas ; avec le soutien de l’Union Européenne via le FCH-JU.
En savoir plus sur « Djewels : plateforme de production d’hydrogène industriel de 20 MW aux Pays Bas ».
Le saviez-vous ?
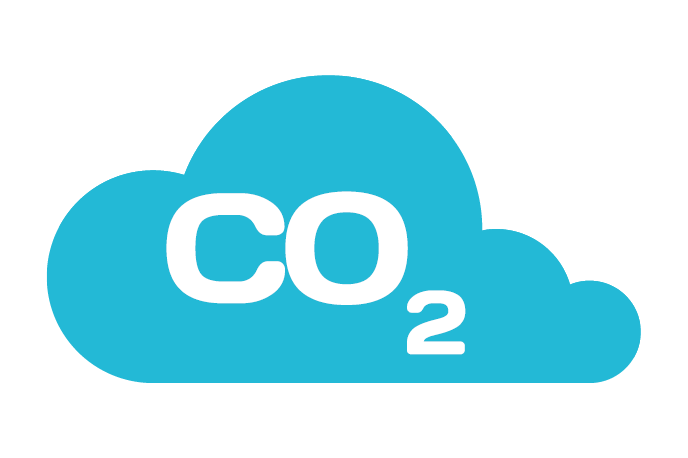
“CCU”
Avec le “Carbon-Capture Utilization”, les émissions polluantes industrielles sont captées avant leur rejet dans l’atmosphère puis additionnées à de l’hydrogène pour créer des molécules de synthèse alimentant de nouveaux usages : e-méthanol, biodiesel, e-fuel, …
Galerie
Vous avez un projet ?
Nous vous conseillons et accompagnons dans le design et la mise en oeuvre
d’une solution hydrogène parfaitement adaptée à vos applications et spécifications.